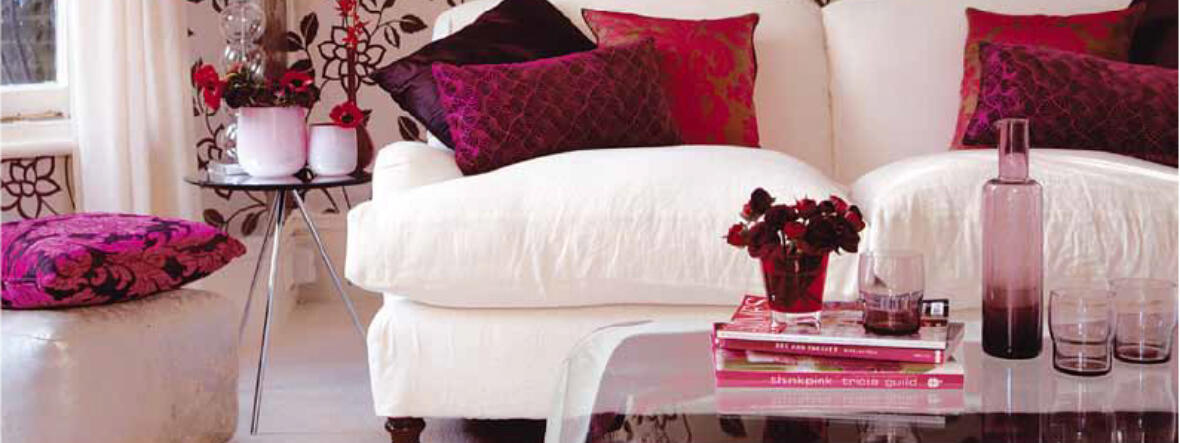
BMSvision wireless system monitors tufting plant at Cormar Carpets
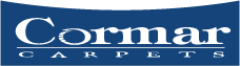
A BMSvision real-time shop floor data capture system has provided significant benefits within six months of installation.
Cormar Carpets installed the latest wireless BMSvision TuftMaster system at its state-of-the-art tufting factory in Ramsbottom, Lancashire, just over a year ago.
“It’s opened our eyes because we hadn’t appreciated fully the enormous benefits it would give us, particularly in improving our machine utilization and monitoring the quality of our suppliers. This definitely has had a positive effect on the bottom line.” said Daniel Ireson, Process Coordinator “Its flexibility is such that I know that we have only touched the tip of the iceberg. There are many more features yet to explore, which will undoubtedly improve our production management even further.”
Background
Historically Cormar only captured how many square metres of carpet it manufactured on a daily and weekly basis. “We knew if a creel was not running well but we did not have enough detail or measurement standards. Consequently it was difficult to go back to a supplier with any proof of where and why we were losing time. Jobs were scheduled manually on a spreadsheet and although we felt that there were opportunities to improve our production capacity, it was a grey area with no real-time or historical data to help us,” Daniel commented.
Cormar wanted to be more competitive and improve its customer service. One of the ways to achieve this was the installation of a specialist, dedicated data acquisition system to identify problems on the shop floor and track the Overall Equipment Effectiveness of the looms. “We didn’t want to have a system developed from scratch and BMSvision was the only company that had a proven data monitoring system for the carpet industry,” said Daniel.
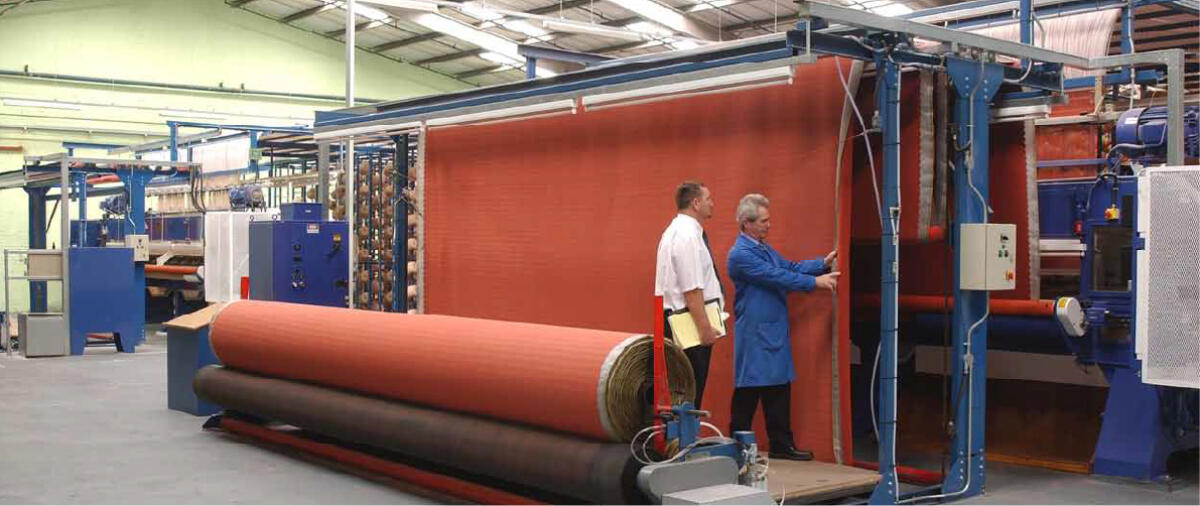
The system
The TuftMaster system connects all of the tufting machines, each fitted with a userfriendly BMSvision DU8P Data Unit. The wireless technology negates the need for running data cables from each tufting machine back to the server, making considerable cost savings. A Bluetooth access point is installed in the ceiling of each of the tufting areas and these units pass information to and from the TuftMaster system using secure Bluetooth wireless RF communications.
TuftMaster provides users with the tools to monitor productivityof Cormar’s tufting machines in real-time and create ad-hoc reports, enabling a quick response where necessary. The userfriendly ‘drag and drop’ planning tool optimizes the loading of the tufting machine and makes the job schedule clear and easy to understand.
A link to Cormar’s TROPOS business administration system eliminates duplication of data entry by automatically downloading production requirements to the TuftMaster system. Similarly at the end of a job change, shift change etc. TuftMaster can back-flush key production data, such as job status against plan, metres produced, efficiencies etc., providing an effective real-time update. Daniel explained. “By creating the link with TROPOS and sending the information back in real-time from the TuftMaster system, we will have all the information we need to give our customers a date for delivery. We know that our quality has improved since TuftMaster was installed because the number of customer service calls has reduced significantly.” In the first year Cormar has focused on machine efficiency. “Before we installed TuftMaster we knew we had a business within a business. It was just a question of identifying where it was. Now that we can monitor in real time the OEE of every machine, the reason why it has stopped and for how long, it has enabled us to identify and respond to problems much more quickly. This has resulted in an improvement of machine utilization, freeing up capacity, so that we don’t have to invest in new equipment for the moment,” Daniel pointed out. “Currently the only standard we monitor is quality against suppliers but we do plan to introduce other standards against which we can monitor change-over time, time spent to repair, time spent on maintenance etc.” he added. Cormar buys its yarn from a number of suppliers across Europe and using TuftMaster they were able to compare their respective yarn performances. “By working closely with these companies they will make improvements and create new standards” he
added.
As Process Coordinator, one of Daniel’s roles is to drive the system forward through the company’s policy of ongoing continuous improvement. “There are a lot of facilities in TuftMaster that we want to exploit. Daniel added, “Staff on the shop floor are fully aware that the machines are being monitored. The teams can access the system to view the OEE of the machines they look after. They appreciate the benefits of TuftMaster because the more efficiently the machines run, with fewer stoppages and less needle breaks etc., the easier it is for them too.”
Benefits
“Now that we are appreciating what these benefits mean to the company, its customers and the effect it is having to our bottom line, it is a really good impetus to move the project to the next stage.”
About Cormar Carpets
Cormar Carpets is the largest independent carpet manufacturer in the UK. It was set up by Neville Cormack OBE in 1956 and now employs 220 people at two production sites in Lancashire. It prides itself on being able to make, back, cut and deliver carpets in its own fleet of vehicles within 48 hours of receipt of order. Although best known in the domestic market, where over a million people choose a Cormar carpet every year, the company also has a substantial commercial business, supplying carpet for high profile building projects like the new Arsenal stadium