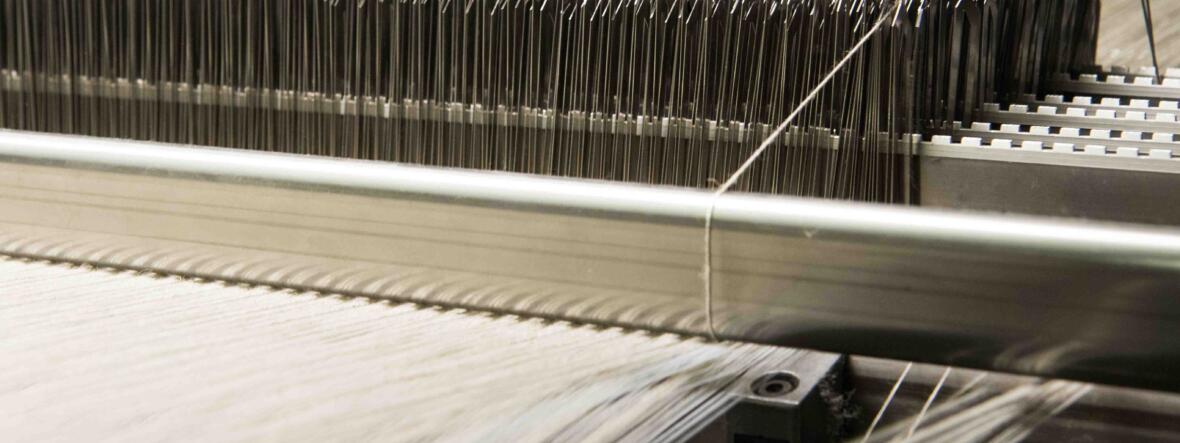
EnergyMaster reduces energy costs at GTA Belgium
Global Textile Alliance Belgium found that EnergyMaster is the perfect tool to produce sustainably and to reduce energy costs.
Produce energy efficiently with EnergyMaster
At Global Textile Alliance Belgium, manufacturer of mattress and bed fabrics, sustainability is very high on the agenda. Next to developing eco-friendly products, they are also constantly researching how they can make their production process more sustainable and more efficient. With the help of BMSvision’s energy management system they can live up to and monitor these expectations.
Without BMSvision’s EnergyMaster we would never have been able to calculate our savings.Safety & Environment Manager
Managing energy rationally: measuring is knowing
One third of the total energy consumption in Flanders is consumed by industry. Through the Energy Policy Agreement (EPA), Flanders is trying to introduce industry to energy management and thus increase energy performance. In exchange for this effort, companies receive a tax reduction and a free energy audit mapping their energy consumption. A real win-win situation.
To understand a
company’s energy balance, there is a need for data, lots of data. The energy
audit at GTA Belgium revealed that their existing monitoring system did not
gather enough information. It only allowed them to monitor electrical energy
consumption. With this, the system did not meet the demand of the EPA where the
current and historical energy consumption of the production processes and the
different utilities have to be identified. Since GTA Belgium’s production had
already been monitored for over 25 years by BMSvision’s MES system WeaveMaster,
their energy management system EnergyMaster was chosen. With the help of this
software, the different energy flows (water, gas, compressed air, electricity, …)
of the company could be mapped accurately and energy saving measures could be
calculated numerically.
Our previous system did not allow to measure different consumption items. So, installing EnergyMaster meant a huge leap forward. We now have a real-time overview of how much energy is consumed, by which machines and when. Before, I had to manually record meter readings on a periodic basis. Fortunately, this time-consuming work is no longer necessary because this data is now automatically stored in EnergyMaster. Now I can fully focus on analyzing energy consumption and through automatic alarms and reports I can react much quicker.Safety & Environment Manager
Reducing costs and CO2 emissions
Being able to intervene immediately in case of excessive energy consumption and, above all, having insight into the company’s biggest consumers is now more important than ever in the current energy crisis. The biggest production cost in the textile industry is compressed air consumption. It was therefore very important for GTA Belgium to be able to monitor the exact cost of this per department. With the installation of strategically placed compressed air meters, it is now possible to precisely break down and monitor the consumption per department. Consequently, these Energy Performance Indicators (EnPI's) are closely monitored. If they no longer follow the usual pattern, any new compressed air leaks are sought during maintenance.
By having accurate data on the energy consumption of their production processes and the base load of the current compressors through EnergyMaster, they were able to work with the manufacturer to calculate the investment in new compressors much more accurately. Due to market evolution, the compressor fleet was no longer dimensioned for the current production processes, which meant that the optimum efficiency of the compressors was no longer achieved.
With the investment in new frequency-controlled compressors including their dryers, the energy efficiency increased by 10 and 72% respectively, resulting in savings of 800 MWh or 320 tons CO2 on an annual basis. In addition, the new compressors required less cooling, allowing the cooling tower to be switched off. An additional savings of 280 MWh or 110 tons of CO2 per year. Today’s energy crisis means that this investment was repaid even faster.
Conclusion: energy management pays off
Since the EPA story and the investment in the compressors, senior management has also been convinced of the energy-saving possibilities that can be accurately monitored thanks to EnergyMaster. Based on the production and energy figures, ideas arise during the weekly production meetings to optimize processes without sacrificing quality. Insight into energy consumption not only pays off financially, but it was also necessary to obtain the STeP certificate (Sustainable Textile Production) in which energy performance and energy management are two important pillars.
Meanwhile, the savings at GTA Belgium have been phenomenal: “EnergyMaster ensures that energy-saving efforts can be measured immediately, which is very motivating. Not all the tests we perform are immediately useful, but they do provide insights on which we can build further. Meanwhile, we have already implemented about ten successful energy-saving measures, good for 2200 MWh or 800 tons of CO2 on an annual basis. Every morning the production managers receive the energy performance indicators for their department in their mailbox. Deviating data are immediately noticed and then we can figure out how to avoid them in the future. Thanks to EnergyMaster, we are constantly aware of our energy consumption,” concludes Martine Baele.
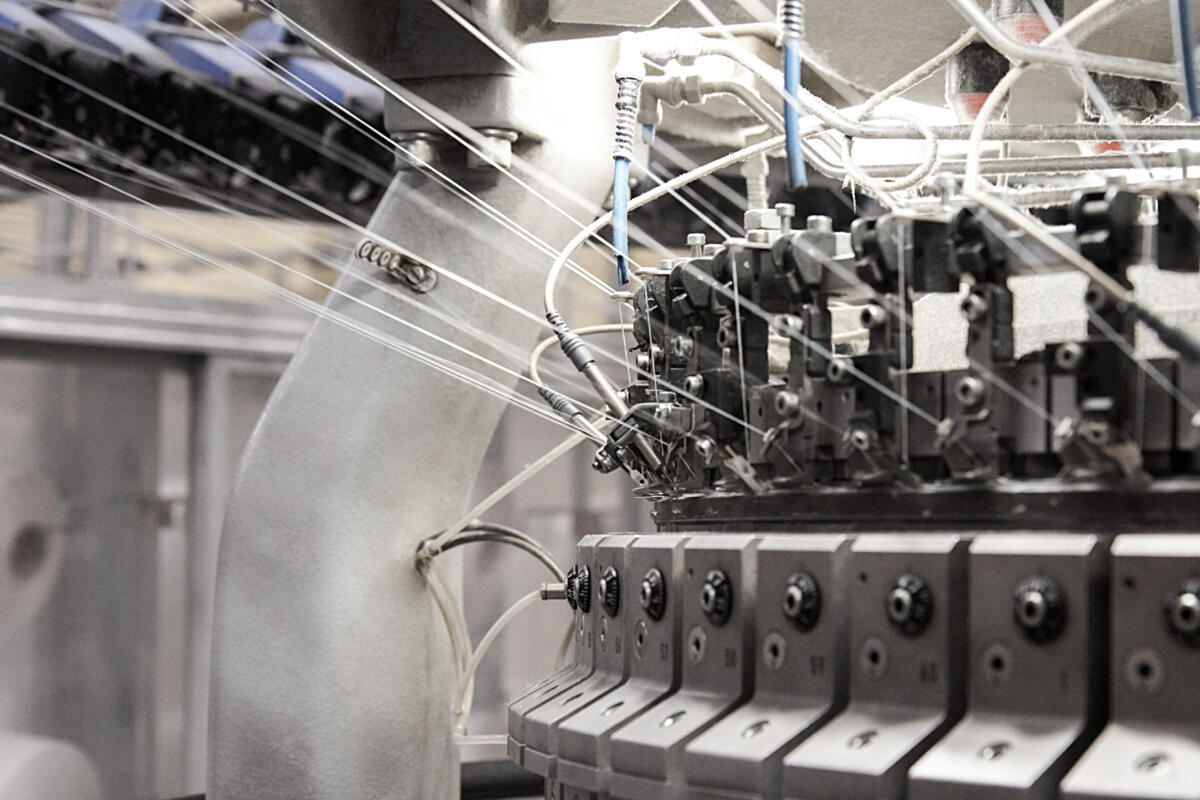