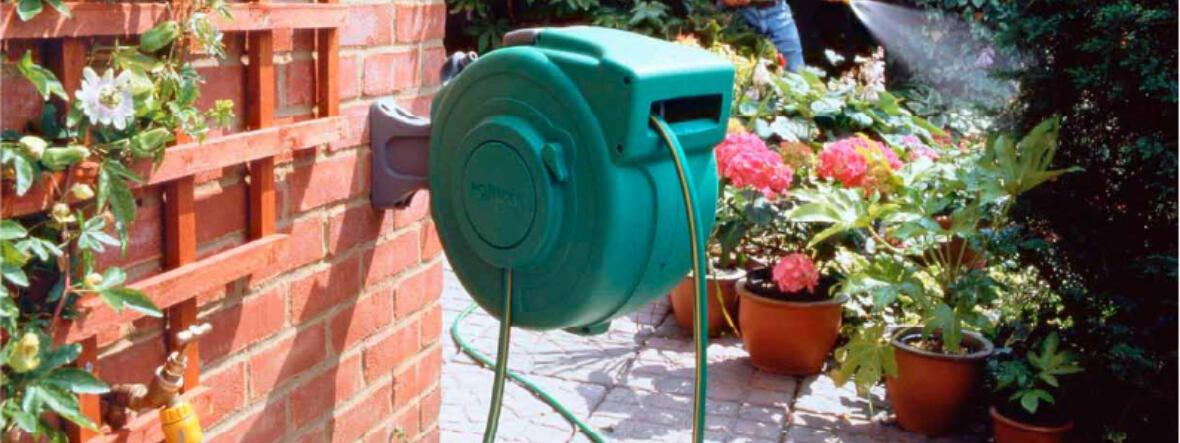
Hozelock upgrades real-time system

Hozelock, manufacturer of garden and aquatic equipment, is one of the first companies to upgrade to the PlantMaster real-time machine monitoring system, BMSvision's new generation MES (Manufacturing Execution System) for the plastics industry.
This powerful and flexible production management tool now uses the Microsoft Windows® operating system with Oracle® as its relational database. Hozelock has now upgraded its production monitoring system twice in the last fifteen years.
“We have an efficiency target which we are always looking to improve with new initiatives,” said a spokesman. “We installed an original Dextralog system about fifteen years ago, which monitored sixteen of our smaller presses at another unit in Aylesbury.
This system was then extended to monitor the larger presses at our main site and then upgraded three years ago when we installed the PC-based PlantMaster system, which gave us real-time monitoring."
"The BMSvision system made a big difference to our machine utilisation and along with several other initiatives increased our efficiency from 75% to over 90%.”
Optimise production
”In 1999, Hozelock decided to upgrade a second time to the latest PlantMaster system which collects a variety of production data from the machines and automatically produces user defined reports using a Windows® Graphical User Interface GUI). There is also a new user-friendly planning board.
“The shop-floor can react much more quickly to sales requirements if we can optimise our production capability and have all the production information at our fingertips. This is where PlantMaster really scores. The real-time ‘drag and drop’ planning board not only allows us to see the work status of each machine, it also enables us to use planning tools to optimise work flow. For example, it will automatically highlight jobs with the same tool, material, or colour to enable the planner to maximise machine use and minimise downtime.”
Hozelock has 60 presses monitored with PlantMaster that range from 25
to 650 tonnes. They use both two-shot and gas injection moulding, producing in excess of fifteen million parts per month which are shipped to the Birmingham factory for assembly.
Each press has a DU5P Data Unit with a text display into which machine status codes can be entered to record all aspects of machine performance.
The Data Unit also allows scrap entry types for product quality analysis. User workstations are located in the Mould Managers’ office, in the maintenance and planning offices, on the shop floor and at the remote site which monitors the 23 smaller machines via a modem link. Each PC operates via a menu system and has a view facility to the PlantMaster file server via the Hozelock PC network.
The BMSvision system made a big difference to our machine utilisation and along with several other initiatives increased our efficiency from 75% to over 90%."
Hozelock can access a live plan of the shop floor at any time showing all the presses. The colour of the press on the screen denotes its current status and they can change any of the parameters they want to observe. The viewing screen allows them to monitor several parameters for each press at any one time. They can see at a glance theoretical speed against actual, stop hours against production percentage and check that cycles run within agreed tolerances.
Individual presses will also alert the PlantMaster user on screen to warn that a job change is approaching or is near the end of its planned production time. This is important because one operator has to look after seven presses.
Their representative said, “I take all my efficiency figures from this system. Now that we have the Oracle® database I can identify when a machine has a problem and provide historical evidence, whereas in the past the system only kept the data for seven days. We printed out reports weekly but with Oracle® I no longer have to wade through sheets of paper if I need to analyse performance information and material usage.” The Oracle® data base at the heart of PlantMaster is Open DataBase Compliant (ODBC) which means it is possible to link with other management systems. “Our goal for the future, is to link PlantMaster to our QAD-MFGPRO system which is operational on all the sites so that we can co-ordinate the data from both systems and outline the capacity plan for a whole season in advance.” In doing so Hozelock will complete the systems integration cycle enabling information to pass from the management system, down to the shop floor and back automatically.
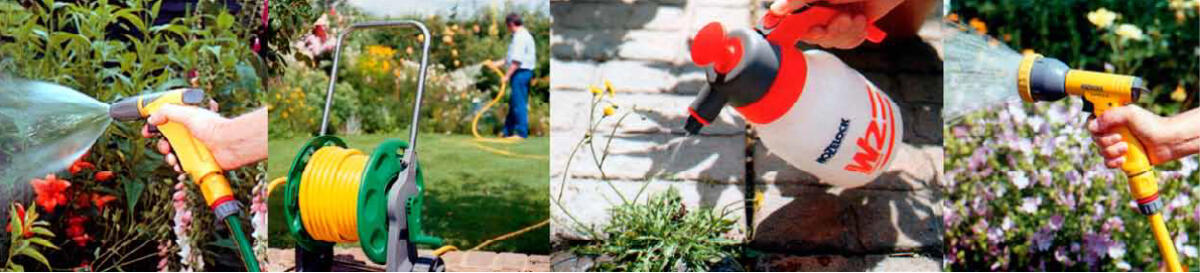