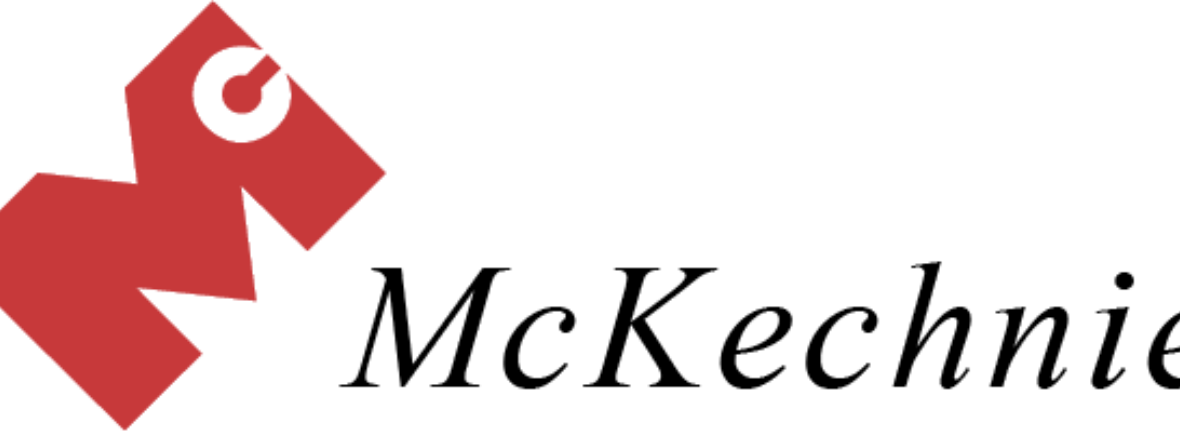
Trade moulders monitor production and energy consumption in real-time with PlantMaster
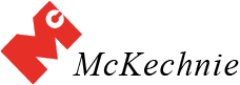
The energy tax (Climate Levy Charge) is a catalyst for many companies to evaluate ways of reducing their energy consumption. McKechnie Plastic Components took the lead recently when they were one of the first trade moulders to install a system that monitors both production and energy consumption in real time.
The Stamford Bridge factory, which installed the PCMS real time machine monitoring system from BMSvision, is one of over sixty sites worldwide in the McKechnie Group. It uses a variety of polymers to mould a wide range of products for customers in many market sectors, including electronics, power tools, packaging, leisure and consumer durables. The company also won the Guinness Supplier of the Year Award for the plastic widgets which are in the bottom of every can of the velvet brew.
Next, they upgraded PCMS to PlantMaster, BMSvision’s new generation of MES systems for the plastics industry, which is faster and has given them many more features. This powerful and flexible production management tool now uses Microsoft Windows® as its operating system and Oracle® as its relational database.
Significant savings
The investment in the original BMSvision system was as a direct result of a report produced by a consultant from ETSU who was called in to monitor the company’s energy efficiency. Until that time McKechnie had made several ad hoc attempts to reduce energy expenditure but had not initiated any formal energy management procedures. ETSU’s findings revealed that 85% of the energy consumption was being used by the injection moulding machines. They maintained that significant savings could be made, but to achieve this, the company needed a clearer picture of the patterns of energy used throughout the factory. Information from the single electricity meter of overall energy consumption would not suffice. There was also a strong belief, which has subsequently proved correct, that energy savings could only be sustained if those involved in managing and running the plant were made accountable for the energy consumption associated with their actions. The only method of achieving such accountability was to install meters on each machine.
Flexibility
The company already had a long standing working relationship with
BMSvision, having used their production monitoring system for many years. As well as being able to monitor both production and energy consumption in real time, BMSvision was also able to solve another problem. As the operators move around the gate area of the press it is not convenient for them to have a fixed control box, so they installed the DU5P data collection units on a portable stand incorporating a fly lead with a flexibility of four metres. Today all 76 injection moulding machines ranging from 35 to 1000 tonnes are monitored. Six new machines are on order and will also be added to the system.
Justin Addison, Business Systems Administrator, was tasked with upgrading the system.
“Technology has moved on since we installed the PCMS system and we were ready for an upgrade. The impending climate levy charge focused our minds once again on the importance of energy saving. Now that we have the PlantMaster system and are putting maximum effort behind the project, the results are beginning to pay off. Our savings efficiency target is 90% on energy usage. The shop floor understands that the meter is running all the time and we can pinpoint areas where savings can be made”, Justin stressed. “It ranges from simple things like turning the machines off when they are idle for any length of time because the BMSvision system informed us that it costs only one third more to run a machine in full production than it does to have it switched on.
PlantMaster also tells us how much energy is required to convert 1 kilo of
material on an average cost basis and how much energy is costing us on each shift from which we obtain daily, weekly and monthly reports.”
One of the other major advantages is that being Windows® based, more people are being trained to use the system. The company now has fourteen licences which means that all key personnel have access to the system. “The new system is much faster, easier to use and produces all the reports we require using a Windows® Graphical User Interface and the Oracle® database”, said Justin. There is also a new planning board which is updated every week.
On the production monitoring side, it has allowed the company to optimise the cycle times of the presses, including the mix and moulding times. It also has scrap reporting analysis. There are fourteen stop codes on each box for production monitoring and a further code to monitor rejects for recycling. Alongside each press there is a Key Points Chart, which alerts the operators to the points that they have to check. If they reject a component for whatever reason, they have to enter the relevant code into the DU5P Data Unit.
Efficiency on target
It’s on the finishing side that there are the most exciting new developments. Two large numeric display boards monitor the two testing sub-assembly lines. The operator logs each pass by pressing a button. It comes up on the board which displays the current number of components tested, the target, the last shift, the efficiency percentage and the weekly total. “It works well because each operator can see at a glance whether the line is on target and it has introduced an element of competition between the two finishing lines” Justin commented. The system will also be integrated into the Impact tool maintenance system so that McKechnie can plan its in-house refurbishment programme. PlantMaster will keep a record of the number of impressions each tool has made so that after a certain amount of lifts it can be taken to the tool room for stripping.
They are also upgrading their current MRPII system to an ERP system. Data generated from it will automatically be transferred to PlantMaster which will produce a work to do list, a pick list and a job schedule for each machine. “BMSvision has done all the hard work in transferring the data from PCMS to PlantMaster. The key to its success is in setting the system up to provide the right information in the first place and training personnel to maximise these benefits. It’s an ongoing process but we will certainly reap the rewards with the control and the data it provides.”
PlantMaster tells us how much energy is required to convert one kilo of material on an average cost basis and how much energy is costing us on each shift