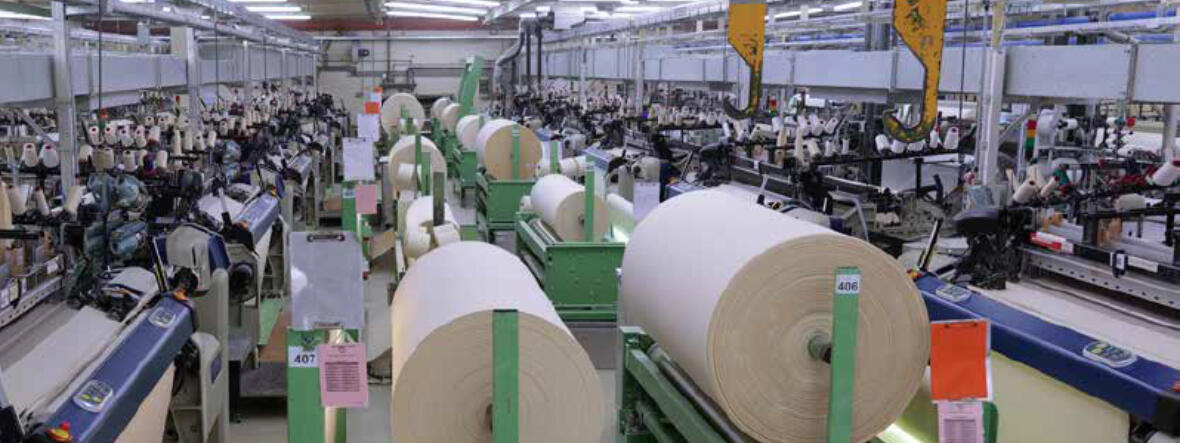
Bringing the best of MES systems to a state-of-the-art family-run business
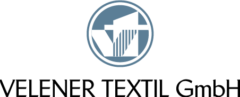
WeaveMaster contributes to high-quality and customized fabric processing at Velener Textil GmbH
Velener Textil GmbH, a family owned company located in Germany produces high quality yarns and woven fabrics. With the latest machine technology in spinning and weaving, Velener Textil produces finest yarns (for processing e.g. table and bed linen) and fabrics (for home textiles, technical textiles, protective clothing) for the European market.
Today’s Velener Textil GmbH, originally founded in the 1930’s, was able to withstand the radical changes which took place in the European textile industry over recent decades, making it a successful and sustainable supplier for the technical textile industries as it is today.
Continuous innovation and automation are two important drivers of this evolving process.
BMSvision is happy to have been able to contribute to that success, by implementing its WeaveMaster MES system on the production floor, tailored to the company’s management needs.
Indeed, the entire grey fabric production floor, from yarn inventory, over warp preparation area and airjet weaving department, up to grey fabric inventory relies on BMSvision’s latest production machine monitoring hardware and the related MES software applications to assure a smooth production process.
Velener’s special request to monitor and document the flow of goods through the production chain, to be able to trace the raw materials used and the requirement to know the current status of the styles and orders to be produced at all times, is handled by BMSvision’s traceability module.
Objective
Before the implementation of the BMSvision MES system, Velener relied on a customized production monitoring system developed back in the 1980’s, tailored to the needs of that time. As development on this system stopped, and as procurement of hardware and related components became progressively difficult, the overall system reliability started to decrease. Because of this and in view of Industry 4.0 with its associated challenges, the search for a modern and powerful system became increasingly urgent.
Before the implementation of WeaveMaster, overall planning and organization was based on an optimally developed analogue process. With the implementation of the system, yarn, warp and order planning processes were integrated, thus enabling a logical sequence of workflow. In the end, also the time consuming cost control mechanisms that were performed in the company could be eliminated as these were taken over by the system.
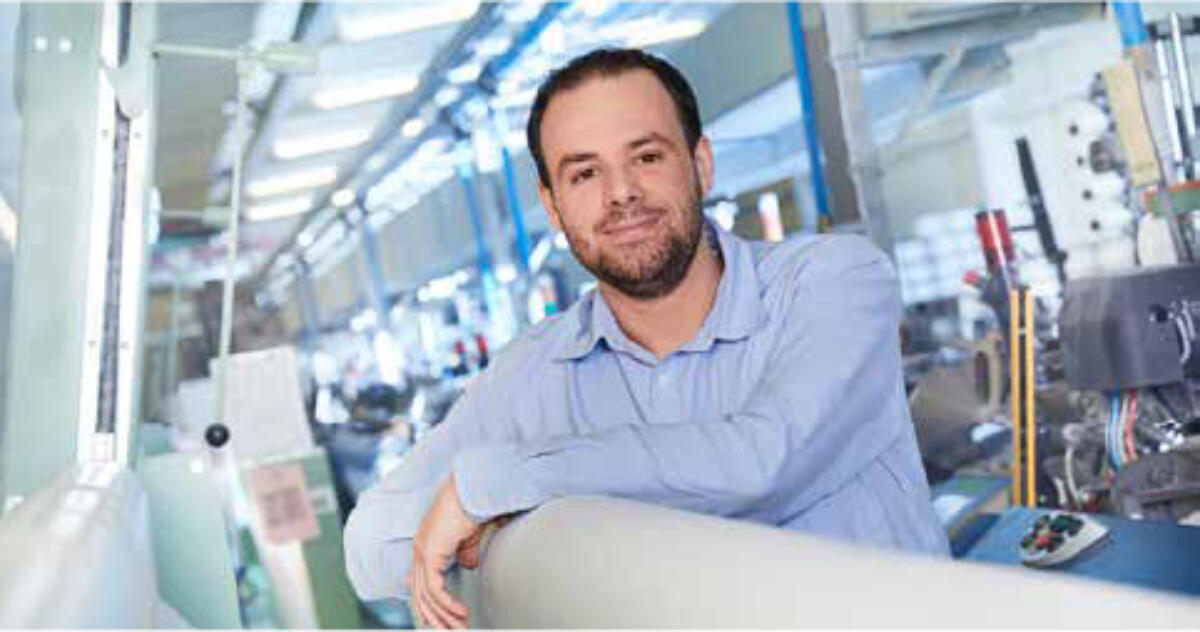
Mr. Thomas Spanderen, Sales Manager Grey Fabrics, “Vertrieb Rohgewebe”
The WeaveMaster system offers all functionalities required for fabric processing in a weaving mill. The high degree of adaptability offers many possibilities to respond to requests and specific events as they occur in the fabric processing chain.”
Finding the right partner ...
In search for a company offering a replacement system, Velener
came across BMSvision, already known to them as a supplier of
proven automation applications for their spinning department.
Among two other possible suppliers on the shortlist, BMSvision
was finally appointed as their partner for the implementation of
the WeavveMastter MES system.
Says Mr Thomas Spanderen: In the end we decided for the elaborate technical system of BMSvision because it can be easily interfaced with the ERP system already in place and because it is able to gradually integrate other processes, such as automatic on-loom inspection and fabric inspection. In addition, the system’s open database structure that can be accessed to retrieve any required information is a big advantage, which makes the system very flexible for us.
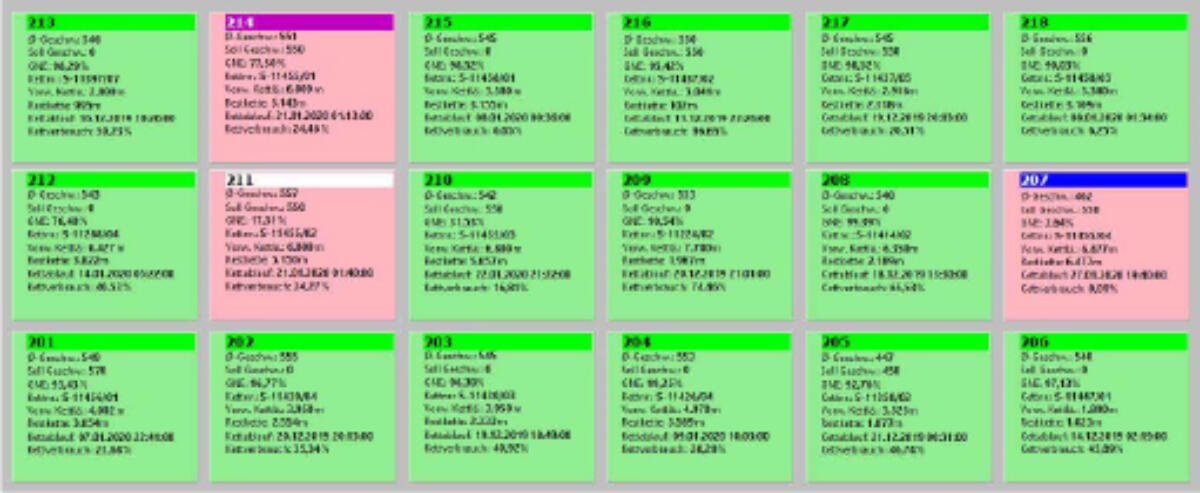
The PlantView shows a color-coded layout of the mill.
This is one of the many examples to present information graphically. It represents a big asset of the system as it immediately draws your attention on alarm conditions such as machines running with poor efficiency, machines waiting for an intervention, etc.
... and implement the best system
Making use of its long standing experience in monitoring solutions for the textile industry, BMSvision could “translate” Velener’s requirement document into a successful solution that resulted in a test system being installed. In a first instance, Velener’s management wanted to experience the look and feel of WeavveMastter, whilst introducing the first information and parameters, without the system already running in real time. In a second phase and for the sake of making comparisons, both systems were running simultaneously, until eventually the old system was shut down and WeavveMastter took completely over.
Of course, the introduction of a new system requires an open attitude towards some new challenges that come along the road.
Mr Thomas Spanderen reveals: “On the technical side of the implementation, we did not experience any problems, and when we introduced the system, we did not have the intention to change work procedures in function of the system. In the course of the change-over, we got convinced that it clearly made sense to follow the specifications prescribed by the system. So, where the production staff used to be more or less free in what order things were done, they adopted the attitude to work by strictly defined procedures, so that data can run properly through the system. This implies a little effort at first, but ends up in very big advantages.”
And Mr Spanderen continues: “This led us to understand the logical complexity of the system (considered in the positive sense) with all its possibilities. As such, we have been able to deploy the system in even more areas than we originally thought, so that everything that concerns direct fabric processing is integrated in one domain.” As an example, it is pointed out that since the system is running, everybody on the floor knows exactly what comes next. When a new warp is required on a machine, it is clear which warp with which warp number is required. The people that are responsible to bring the woven pieces into the warehouse can read from the label where it has to be stored, or that it has to go to the inspection department. The system also keeps up with yarn purchasing and planning, as it is perfectly known which amount and which type of yarn will be required for the coming weeks, resulting in more accurate purchase orders. Generally spoken, the system has allowed to set up a time- and cost saving way of processing.
It is obvious that during the implementation, some processes have to be adapted to streamline procedures and make them more secure. In our organization for example, we have introduced a yarn code system (with yarn numbers). This required some “get used to” attitude from our production staff, but in the end, the risk of mix-ups could be considerably reduced.”
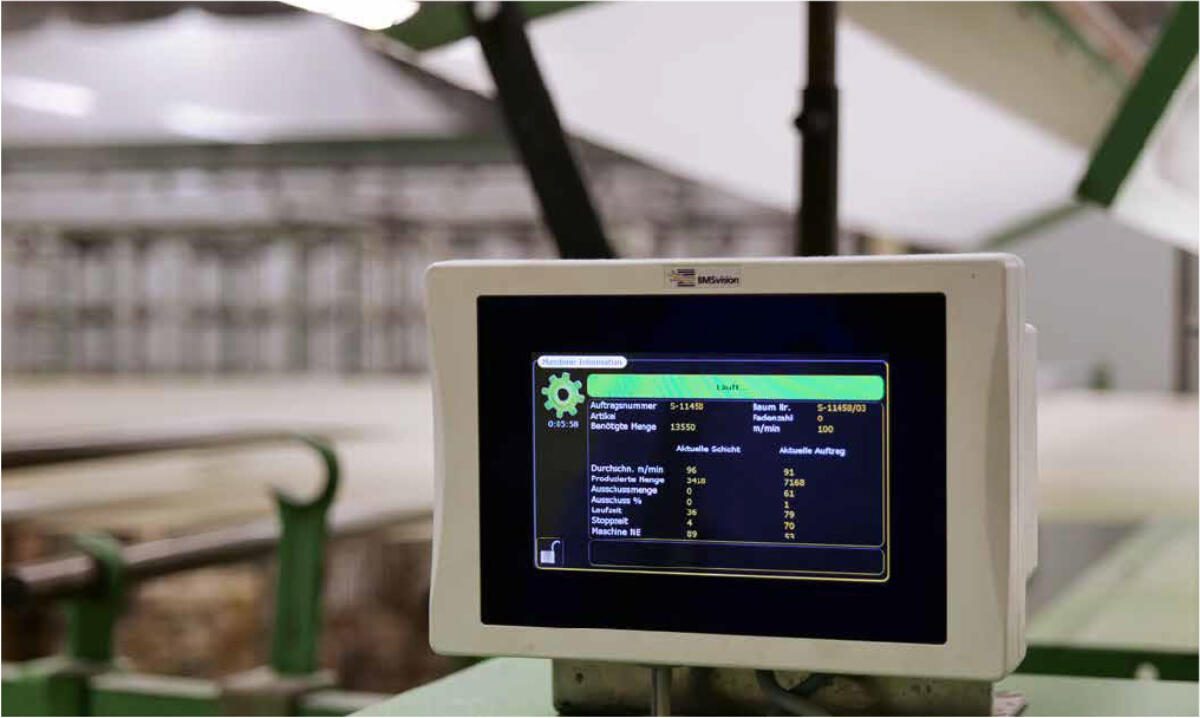
The BMSvision DU11 terminals with 7” touch screen, installed on the warp preparation machines running at Velener transmit machine monitoring data such as speeds and yarn breaks to the WeaveMaster Windows server.
The implementation of the system has proven to be an important asset for the ongoing success of Velener Textil. Thanks to the joint effort of both parties, combining Velener’s ongoing innovation strategy and the expertise of BMSvision in terms of MES systems, Velener recently took the next step in their automation project: the QuualiMastter fabric inspection and quality management module was integrated into the existing BMSvision MES environment, interfacing to the Update Texware ERP system for automatic data transfer.
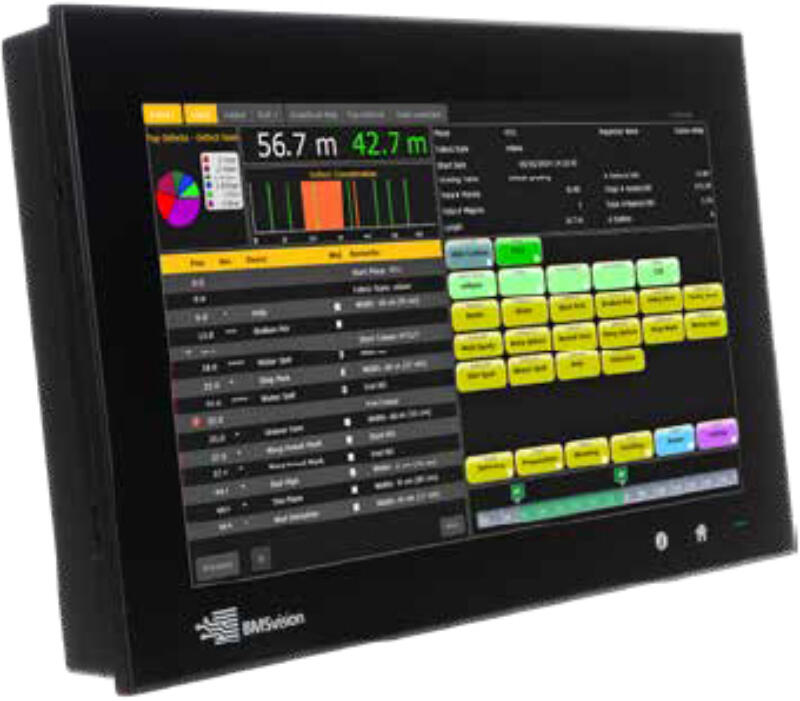
The touch screen PC-based terminal (so-called QT-terminal) connected to the fabric inspection frame, allows defect entry and real time display of the piece map. The included interface unit can drive peripheral devices, such as a label printer for printing piece tickets.
All defect information is stored in the history database to allow a large number of quality analysis reports such as detailed piece map, grade per style/customer/inspector, pieces and meters inspected per time frame, etc. After a piece has been fully inspected, it is possible to print an inspection report in the customer’s language, to determine the quality grade of every piece, ...
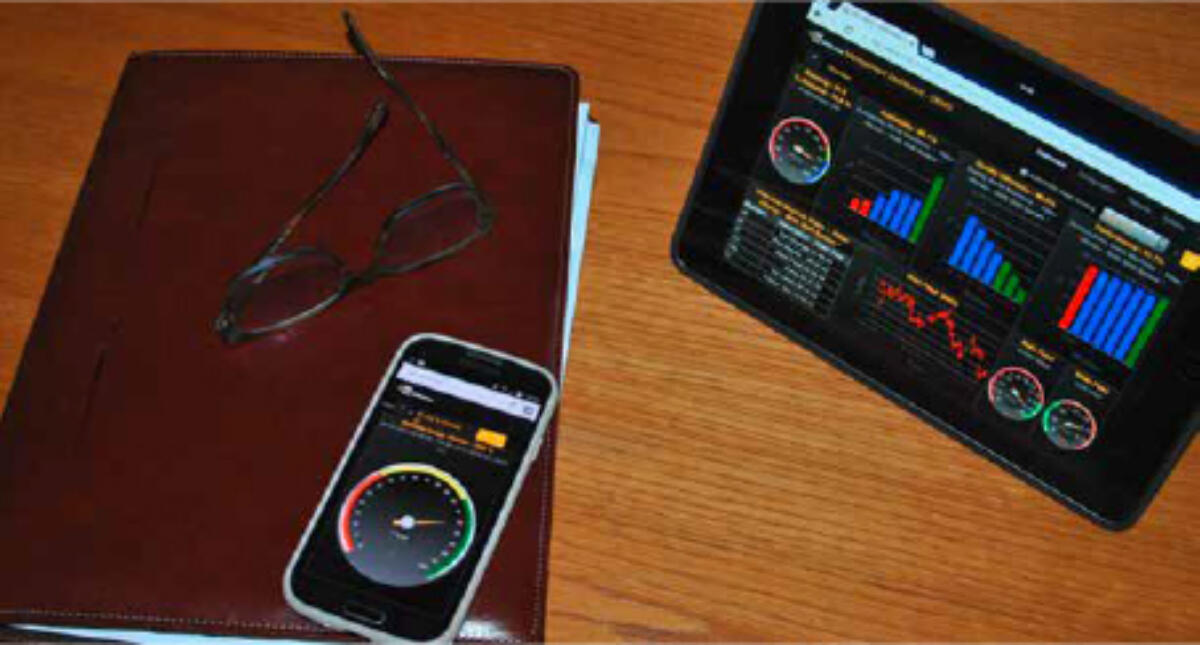
Every step in the buying process, from the very first contact until the final acceptance of the implemented system, has been very professional. We are very satisfied with the good after sales support which is well organized with the Service Level Agreement. For any problem or any question, an on-line help desk ticket is filed, and the reported issue gets answered and solved very quickly.
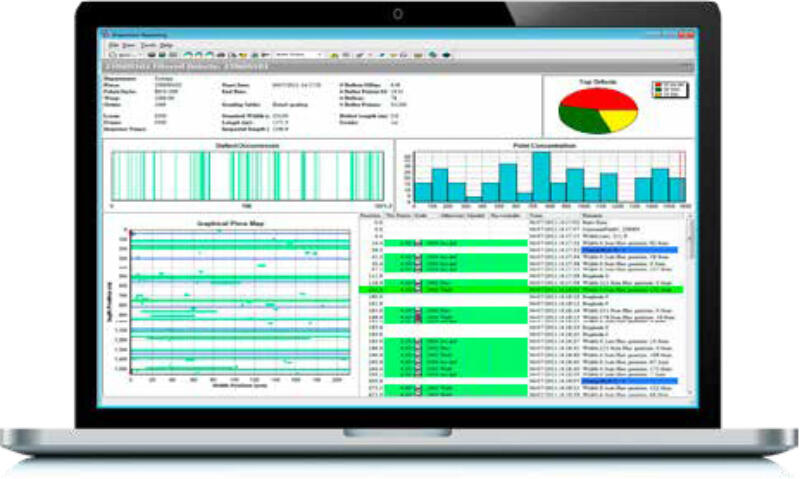
At the same time, also the Management Dashboard module has been implemented. This allows the combined presentation of any data available in the installed application modules running on the Velener production floor into one single web based report. As such, Velener’s management can have all important information regarding efficiencies and quality information displayed in real time on one single screen.
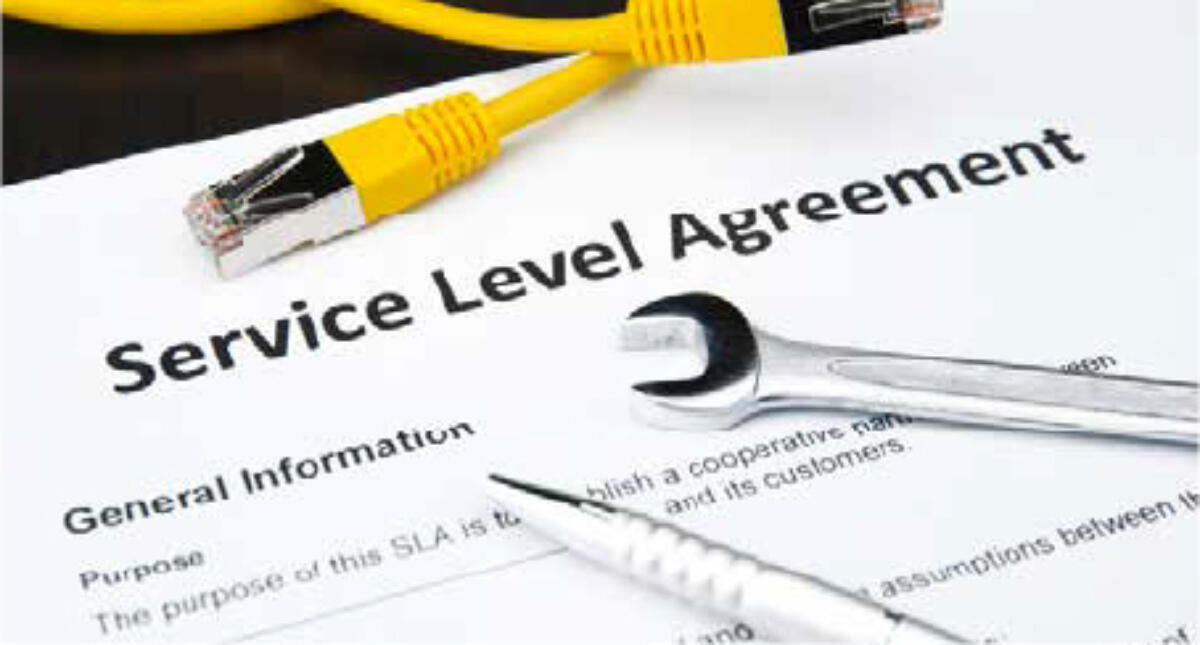
Conclusion
With all machines being linked and read out, and with systems being interfaced, Velener Textil GmbH tackles the challenges of the Smart Industry. There is an excellent insight into what is happening on the production floor and processes can be optimized more quickly, which results in shorter lead times and work being done more efficiently. In the end, this allows to better respond to the requests of the increasingly demanding end customer.