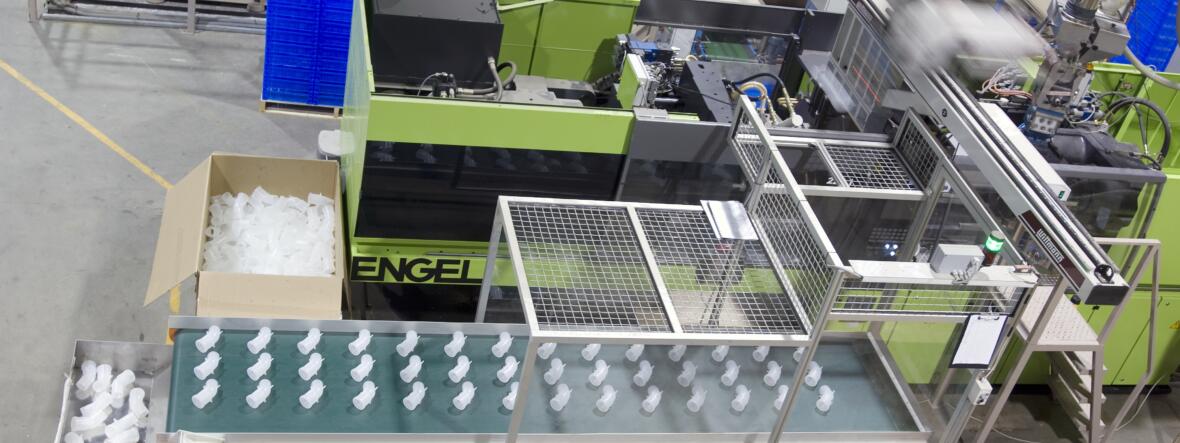
Hollarts Plastic Group consumes energy efficiently
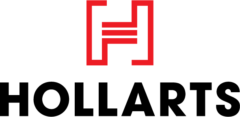
Hollarts Plastic Group, located in The Netherlands, is an ambitious player in the plastic injection molding market. With 30 injection molding machines they produce a wide variety of products, mainly for the logistics market. An important focus point of Hollarts is sustainability.
Consume energy efficiently with EnergyMaster
At Hollarts, sustainability is not just limited to the raw materials used or the circularity of the end products, it encompasses the larger process. Plastic injection molding is a very energy intensive process, so naturally Hollarts doesn’t want to be careless with their energy consumption. After taking some initial steps like placing solar panels on their roof buildings and replacing the fluorescent lighting in their buildings with LED lighting, Hollarts wanted to do more. They wanted to optimize their energy use to lower their environmental footprint and financial costs. "With the help of EnergyMaster, BMSvision's Energy Management system, we are able to map in detail our energy consumption. Thanks to the large amount of data, we can take targeted actions and carry out our energy policy," explains Oliver Goud, Operational Director Hollarts Plastic Group.
Knowing that you want to produce more energy efficiently is one thing, but knowing how to do this is something else.Operational Director Hollarts Plastic Group
Energy policy pays off
Immediately after implementing EnergyMaster in Hollarts’ production process, it became clear that the chillers were responsible for a big part of the total energy consumption in the plant. After analyzing the data, Hollarts discovered that the chiller pumps weren’t adjusted to the number of active machines. Action was taken by installing frequency-driven pumps, which change the water flow in correlation with the cooling demand of the active machines, resulting in a 30% energy efficiency on the chillers’ side.
To pursue a successful energy policy, Hollarts decided to split up the energy consumption according to active production time and downtime so that targeted actions could be taken. This way, for example, operators from the injection machines are immediately notified with the BMSvision dashboard when a machine consumes energy during downtime.
With the data insights from EnergyMaster, production managers and operators will start holding weekly meetings to discuss and learn about the actual energy consumption of the machines during idle time. In combination with PlantMaster, BMSvision’s MES system, the energy consumption on stop code level can be identified, creating the opportunity to prioritize the handling of stops and thus to reduce energy consumption again.
ROI < 1 year
66% of the energy in the plastics industry is consumed by the machine park. When taking a closer look, it was found that 8 – 10% of this energy is still consumed during downtime. When there is an overall energy consumption of 3000 MWh/year, 198MWh is still consumed during downtime. With an average energy
cost of 120€/MWh, 23 760€/year can be saved when energy consumption during downtime is reduced to a bare minimum.
As a result of these data-based insights, Hollarts is more aware of its energy consumption and the need to invest correctly in energy-low machines. These efforts have led to a 20% reduction of energy consumption (from 10000 to 8000 MWh/year).